Nuestro Proceso
¿Cómo se produce el contrachapado Lumin?
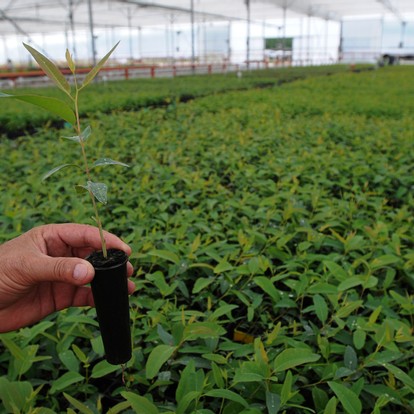
Plantar
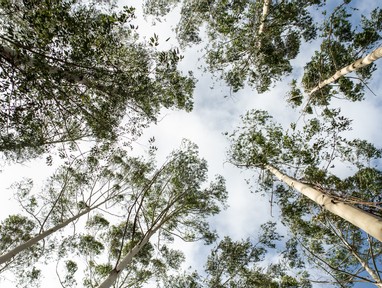
En nuestro vivero producimos plantines de eucaliptos y pinos que seran plantados y manejados con podas y raleos para la producción de madera de calidad
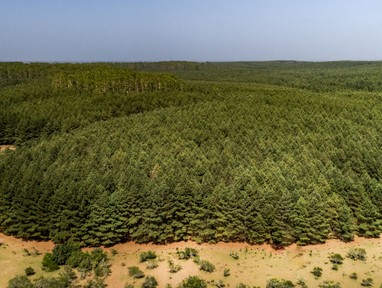
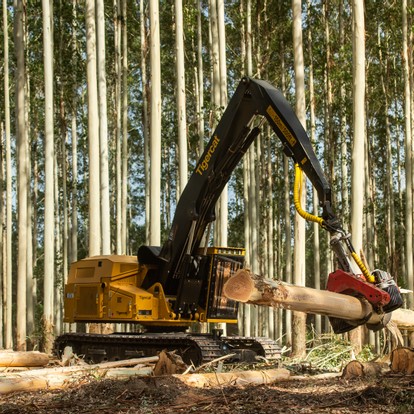
Cosechar
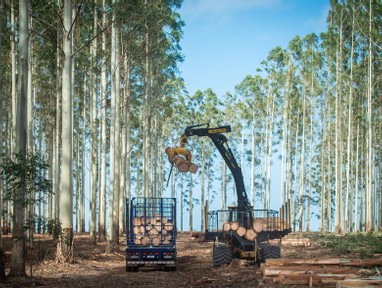
Cosechamos siguiendo un plan operativo que contempla las necesidades de la industria y la maximización de nuestros bosques
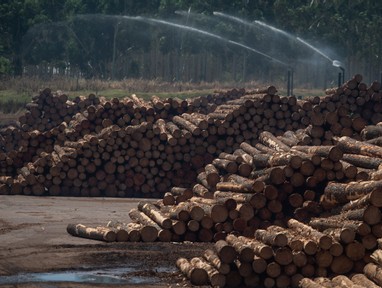
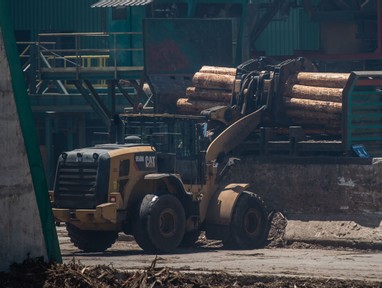
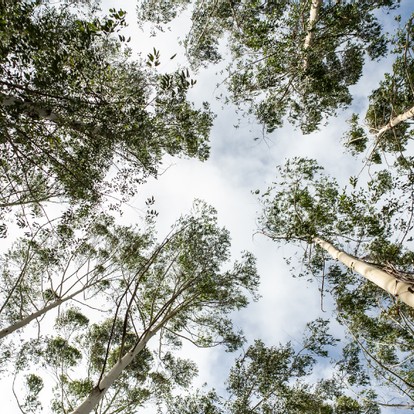
Descortezar
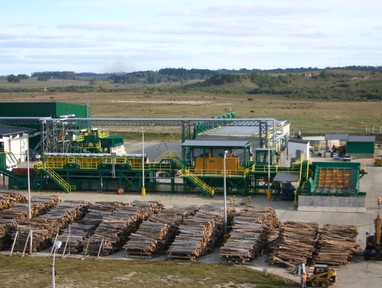
El objetivo de este proceso es quitar la corteza externa de los troncos sin dañar a la madera de los rolos.
Para ello, mediante el empleo de cargadores frontales con grapo, los rolos se retiran de la pila de almacenamiento húmedo y se alimentan a una descortezadora de anillo. Las trozas descortezadas son clasificadas nuevamente por tamaño y diámetro, antes de pasar a la siguiente etapa.
La corteza separada por este equipo, se alimenta mediante el concurso de un transportador mecánico a una trituradora con el objeto de reducir su tamaño de modo que pueda ser usada como combustible sólido para generación de vapor.
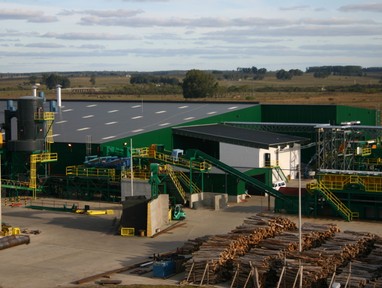
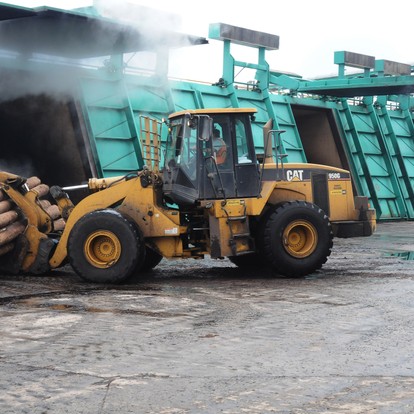
Acondicionar
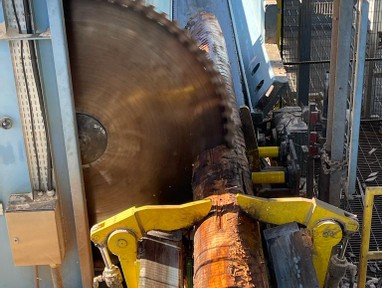
Los rolos descortezados se retiran, con cargadores frontales de las tolvas en que se depositan al completarse la operación anterior, y se introducen en cámaras abovedadas, para rolos de largo doble y para rolos de largo simple, dispuestas en paralelo para realizar su acondicionamiento.
El propósito de esta operación es ablandar las fibras de los rolos y facilitar así las operaciones posteriores.
El agua caliente que llueve sobre los rolos, los calienta y, simultáneamente, va cayendo entre ellos en forma de cascada, hasta llegar al piso de la cámara con pendiente hacia la parte posterior de la misma.
Sierras despuntadoras
Una vez acondicionados, con la ayuda de cargadores frontales, los rolos se retiran de las cámaras de macerado y se alimentan a un sistema de sierras de corte que los despunta (Bucking) de modo de obtener trozos de longitud uniforme, de 2.63 m cada uno, conocidos como trozas. Esta operación se realiza con dos líneas de Producción, cada una de ellas equipada con 3 sierras circulares. Posteriormente se desplazan hacia el torno de la correspondiente línea por transportadores de cinta.
Las puntas de madera resultantes de estos cortes de los rolos para llevarlos al tamaño debobinable (despunte), se desmenuzan en chipeadores y, mediante un sistema de transportes de cadena y cintas, se conducen al depósito de residuos de madera para ser utilizados como combustible sólido para la generación de vapor y energía eléctrica.
Aquellas trozas que por alguna causa no cumplen con los requerimientos del proceso productivo, son enviados a un bin de rechazo, posteriormente pueden ser chipeados y convertidos en combustible o rechazados y devueltos al proveedor.
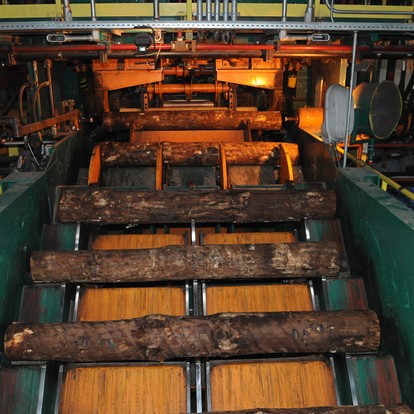
Debobinar
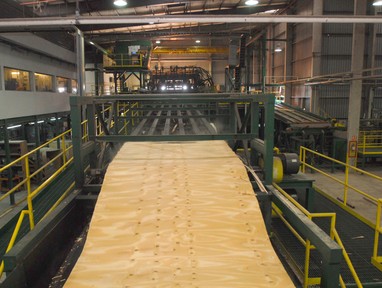
Tornos (3 líneas de debobinado, 8’)
Las trozas dimensionadas, provenientes de las sierras despuntadoras, son acumuladas en las respectivas mesas de acopio y elevadas por un alimentador a pasos que transporta las trozas una a una hasta el cargador XY de los tornos. El cargador XY está dotado de varios sensores Laser, que hacen un reconocimiento de la forma de cada troza, haciéndola girar una revolución (360°) sobre dos puntos de fijación. Luego del reconocimiento, los dos puntos de fijación se posicionan de forma tal que cuando la troza se coloque en los puntos de rotación del torno, se obtenga el máximo aprovechamiento de madera al debobinar.
Cuando la cuchilla se apoya sobre la troza que está girando, se comienza a debobinar una lámina fina continua de madera de un espesor calibrado y deseado.
Una vez pelados las trozas, permanece el corazón cilíndrico nudoso central de los mismos. Para ser empleado para obtener distintos subproductos que incluyen listones separadores para las láminas (tacos) y para el empaque de los paneles de madera laminada obtenidos o, como alternativa, ser utilizados para fabricar pallets o ser alimentado a un equipo triturador para obtener chips a utilizar como combustible para la generación de vapor.
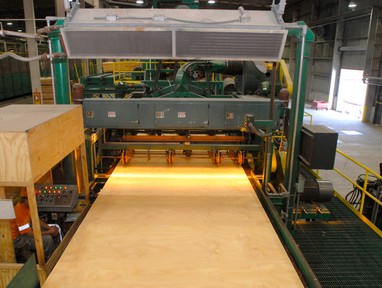
Corte y Apilado (Clipper y stacker)
La lámina continua de madera proveniente del torno (veneer), es analizada por un instrumento denominado scanner, con el objeto de detectar fallas, nudos o roturas en esa pieza continua de veneer. El sistema está compuesto por una cámara, una fuente de iluminación, que permite un análisis continuo del paño de veneer que pasa debajo del instrumento, una guillotina (Rotary Clipper) y un programa de control que acciona la guillotina y corta la lámina continua de veneer de acuerdo al resultado del análisis realizado.
Cuando el scanner detecta algún tipo de defecto en el paño que pasa por debajo de la cámara, comandará a la guillotina para realizar un corte antes y después de la falla, obteniéndose láminas de menores dimensiones (random). Dependiendo del largo resultante, se denominarán media lámina si tuviera un largo mínimo de 0,70m de largo y random si estuviera por debajo de ese valor. Estas piezas de menor tamaño, son derivadas a una mesa de clasificación manual, donde los operadores clasifican las piezas por calidad y ancho.
Estas láminas y tiras apiladas manual y automáticamente, se trasportan mediante el empleo de autoelevadores al área de depósito de láminas húmedas (Wet Veneers).
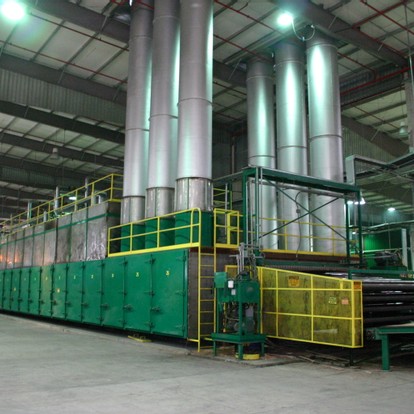
Secar
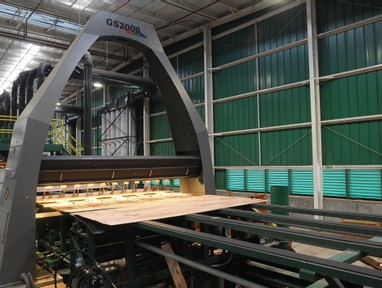
Las láminas de veneer cortadas, ya sea entera, media lámina o random, se introducen en el proceso de secado en paralelo, calefaccionados mediante vapor indirecto con el objeto de reducir su contenido en humedad.
Por lo general, la misma se reduce a valores comprendidos en un rango relativamente amplio, entre 4% y 15%. El secador horizontal de láminas, se caracteriza porque circula aire paralelo a las láminas o porque lo hace dirigiendo aire caliente en forma de chorros a velocidad elevada hacia la superficie de las láminas creando un flujo de aire más turbulento. Ello permite un uso más eficaz de la energía del secador reduciendo el tiempo de secado. Una vez secas, pasan a través de un detector de humedad en base al contenido de humedad y de la calidad de la lámina, se realizan clasificaciones acorde a los requisitos deseados.
Posteriormente son trasladadas a la zona de almacenamiento de las láminas secas. En caso que no se obtenga la humedad deseada, se ingresan nuevamente a uno de los secadores a una temperatura menor para completar el proceso de secado requerido (proceso de resecado).
Composición de láminas (componedoras)
Para aprovechar las tiras o random, se dispone de equipos específicos (Core Composers), cuyo propósito es preparar láminas completas de madera a partir de porciones de láminas secas de largo y ancho definido. La máquina sujeta un borde recto cortado con cuchillas adecuadas sobre los trozos angostos de lámina de madera, aplica adhesivo y une las tiras para formar láminas enteras que luego son sujetas mecánicamente y cortadas en las dimensiones requeridas.
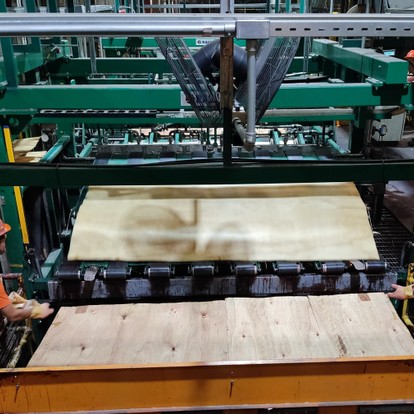
Pegar

Encolado y armado de paneles
Las láminas de madera secas, almacenadas en el área de depósito correspondiente se trasladan, mediante autoelevadores, a una línea automática de ensamblado de tableros, con aplicación de adhesivo por extrusión.
Estos equipos, tienen por objetivo distribuir o aplicar uniformemente adhesivo. Las láminas encoladas de los núcleos se ensamblan con las láminas que constituyen las caras exteriores para dar lugar a los paneles de madera.
El montaje de los paneles de madera laminada debe ser simétrico a ambos lados de un centro a efectos de evitar alabeos excesivos.
Adhesivo
El fenol-formaldehído requerido para el proceso, es suministrado por un proveedor externo, pronto para su aplicación (RTU). El mismo nos permite que los paneles producidos tengan resistencia al exterior y en cumplimientos con las certificaciones de productos mencionados en la página web.
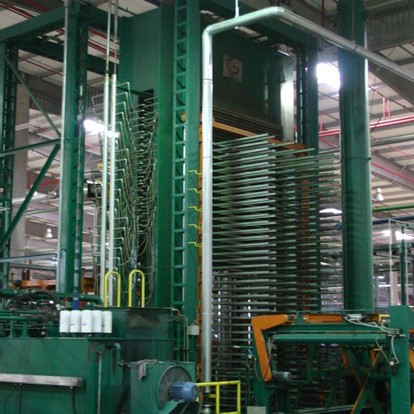
Prensar
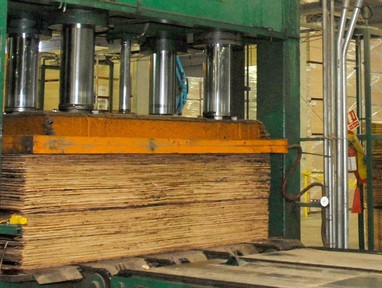
Los paquetes de láminas encoladas y ensambladas se cargan en las Pre-Prensas instaladas antes de ser introducidos a las Prensas Calientes.
Cada Pre-Prensa aplica suficiente presión como para unir entre si las láminas que componen los paneles de modo que éstos puedan ser separados, manipulados y colocados a continuación en forma individual en la Prensa Caliente.
Cada Prensa Caliente aplica presión y calor a los paneles para hacer fraguar la resina del adhesivo y unir entre si las láminas de cada panel. El prensado caliente tiene dos objetivos principales: extender la resina de modo que forme una capa fina sobre cada lámina de madera y activar su fraguado térmico.
El tiempo y la temperatura de prensado varían en función de la especie de madera y del espesor del tablero.
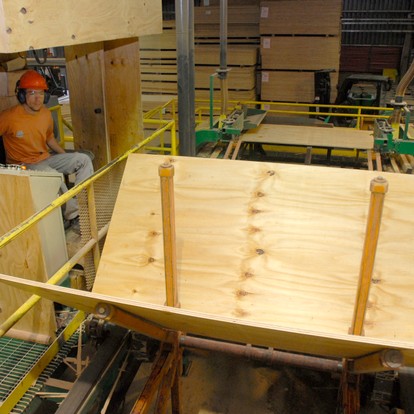
Lijar

Operaciones de terminación. Escuadrado, reparado, lijado y clasificación
Los paneles de madera laminada, se someten por último, a un proceso de terminación en el que se recortan los bordes y las dos caras exteriores se lijan o no, para darles un tacto final suave. El tipo de terminación depende del producto final que se desea obtener para atender los requerimientos del mercado demandante.
Una vez que los paneles se han ajustado en sus dimensiones, pasan por un equipo de ultrasonido (Blow Detector) que verifica la perfecta adhesión de todas las capas del panel. A continuación, un operador calificado inspecciona y define(clasifica) el grado de cada panel. A continuación, los paneles, clasificados por grado de calidad, son apilados automáticamente.
Como consecuencia de esta inspección de calidad algunos paneles se envían a una linea de reparación (Poly Patch) que permite mejorar su calidad mediante relleno de pequeñas fallas y nudos con aplicación de productos químicos específicos certificados.
Posteriormente los paneles continúan el proceso de finalizado pasando al sector de Lijado, donde se realiza el lijado de las caras de los paneles hasta alcanzar el acabado requerido.
Las estaciones de trabajo de todas estas operaciones de terminación disponen de sistemas de extracción del polvo fino que se genera en las mismas para asegurar un ambiente de trabajo satisfactorio y se deriva ese subproducto para utilizarse como combustible de caldera.
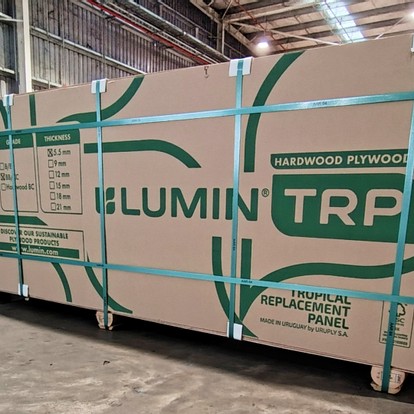
Grado y embalaje
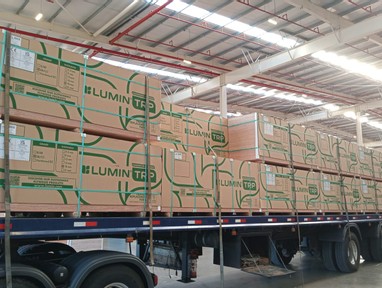
Los paquetes de tableros luego de la última etapa del proceso, reciben diferente preparación para su almacenamiento y posterior expedición dependiendo del destino, cliente y grado de calidad.
Los paquetes pueden ser procesados con diferentes tipos de empaque: film stretch, pintados los laterales del paquete en la cámara de pintura, o flejados con flejes plásticos, dependiendo del grado, destino o cliente.
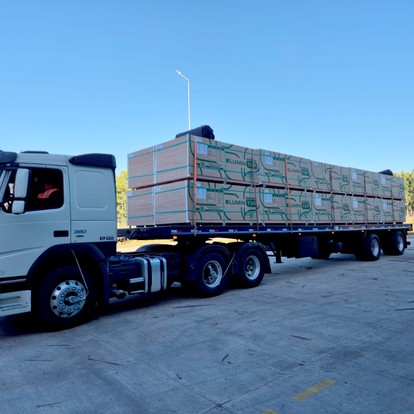
Transportar
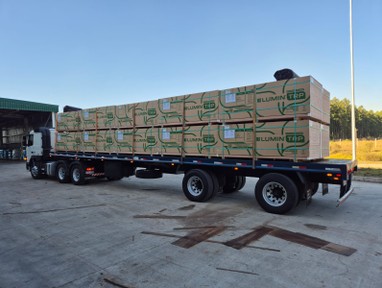
Los paquetes de tableros o láminas pueden ser expedidos de Planta mediante transporte ferroviario o por camión, dependiendo también del mercado, cliente o destino final.